For Wisconsin homeowners, ensuring year-round comfort is a priority. However, many overlook the connection between insulation and HVAC performance. With harsh winters and humid summers, maintaining a manageable indoor temperature without overextending HVAC systems is crucial.
In this guide, you’ll discover the different types of insulation, how they impact HVAC efficiency, and practical steps to improve your home’s energy savings.
Understanding Insulation: Why It Matters
At its core, insulation is a material designed to resist heat flow between the inside and the outside of the home. It serves as a thermal barrier to maintain a consistent indoor temperature regardless of seasonal extremes.
In winter, insulation traps heat, while it prevents external heat from entering the home in the summer. Insulation’s ability to resist heat transfer follows the R-value rating; the higher the number, the better the thermal performance. This is especially important in colder regions like Marathon County, WI, where winter temperatures often drop below freezing.
Choosing the Right Insulation for Each Area of Your Home
Choosing the right insulation is just as important as having insulation in the first place. Different materials perform better in specific areas of the home, and understanding their strengths helps you make more informed decisions.
Fiberglass Batts
Fiberglass batts are a frequently used insulation material in many residential properties. They come in pre-cut panels and are typically in open walls, floors, and attics. While fiberglass is easy to install, you must fit it snugly. Gaps, compression, or misalignment reduce its effectiveness, particularly in older homes where framing isn’t always standard.
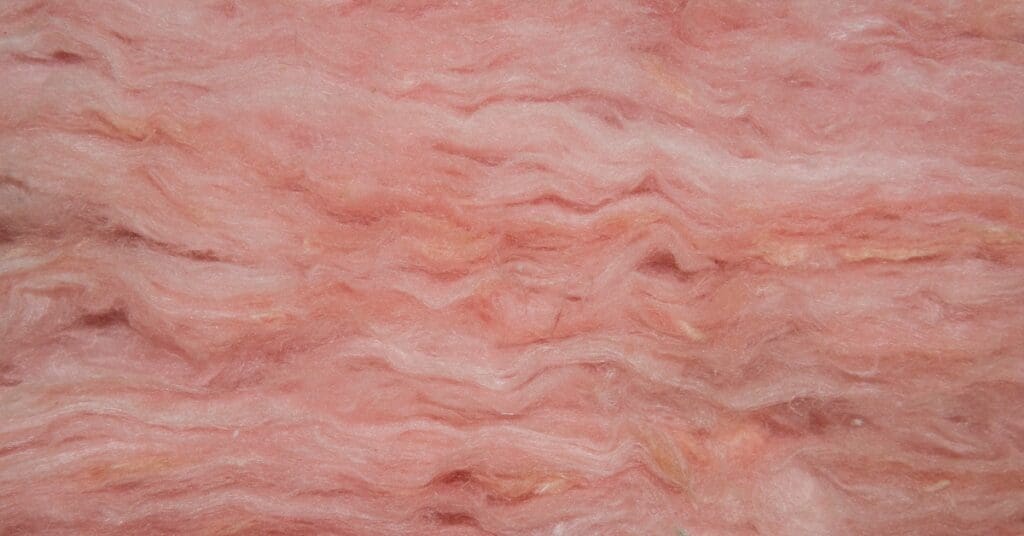
Blown-In Cellulose
Blown-in cellulose offers greater flexibility. This loose-fill material is ideal for adding insulation to existing walls without removing drywall. It fills irregularly shaped areas and small gaps better than fiberglass batts, making it a good choice for retrofitting older homes. In addition, it comes from recycled paper, giving it an eco-friendly appeal.
Blown-In Fiberglass
Another effective loose-fill option is blown fiberglass insulation, which is particularly useful for attics and hard-to-reach cavities. Made from spun glass fibers, this type of insulation delivers thermal resistance while being resistant to moisture and fire. When properly installed, blown fiberglass creates a consistent layer without gaps, minimizing heat loss and reducing strain on the HVAC system.
When attic insulation is underperforming, heated or cooled air escapes easily, forcing your HVAC system to run longer and more frequently. By sealing these thermal weak spots, blown fiberglass insulation creates a more stable indoor environment, which in turn lowers energy bills and extends the lifespan of your heating and cooling equipment.
Spray Foam Insulation
Spray foam insulation is the heavyweight champ for sealing and insulating. It swells to fill gaps and crevices, forming an air-tight barrier to block moisture. Spray foam is most effective in hard-to-reach areas, rim joists, and places where other insulation types might leave vulnerabilities.
This type of insulation comes in two forms: open-cell and closed-cell. Open-cell foam is lighter and more adaptable, making it ideal for interior applications. Closed-cell foam, on the other hand, is denser, offers a higher R-value per inch, and acts as a vapor barrier. This makes it perfect for areas exposed to moisture or extreme temperatures.
Rigid Foam Boards
Rigid foam boards are another versatile option, repeatedly used on basement walls, foundation exteriors, or beneath siding. These panels offer a high R-value and moisture resistance, suitable for insulating below-grade spaces or as continuous exterior insulation.
Each type of insulation brings unique benefits; in many cases, you may have a combination of these materials throughout the home. The key is to evaluate your home’s needs by space and function.
How Poor Insulation Impacts Your Home
Without adequate insulation, your HVAC system works overtime to keep up with temperature fluctuations. In the cold Wausau, WI, winters, poor insulation means your heating system will have to compensate for heat loss, resulting in a spike in your utility bills. In time, the extra stress reduces your HVAC system’s lifespan.
Poor insulation also causes higher humidity levels in the home. Warm, moist air from the outside enters the home, leading to condensation inside walls, ceilings, and windows. This encourages mold and mildew, affecting the health of the home’s residents.
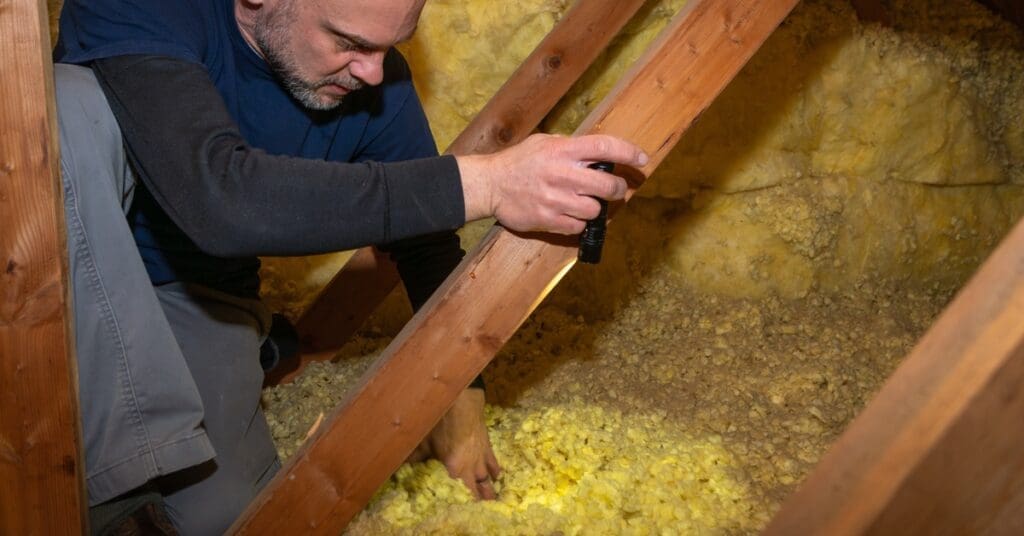
Inside the Insulation Inspection Process
If you suspect your insulation isn’t performing as it should, the first step is to schedule an inspection with residential insulation contractors. A thorough inspection will identify areas where your home is losing heat or allowing moisture to enter. Contractors typically focus on high-risk areas like the attic, crawl spaces, and basement. They’ll check for gaps around windows, doors, and ducts and assess whether the insulation has settled or compressed over time.
In addition, they’ll evaluate the overall R-value of your insulation and recommend improvements based on the home’s specific needs. The contractor may suggest replacing outdated fiberglass batt insulation with more effective options, such as spray foam or cellulose. This inspection pinpoints the best solutions for optimizing your HVAC performance and lowering energy bills.
From Removal To Upgrade: A Look at Replacement
Once you’ve decided to upgrade your insulation, the next step is understanding how the process works. To start, they’ll remove the old or damaged insulation. This involves vacuuming loose material or manually extracting batts, depending on the insulation type.
After cleaning and drying the area, contractors will seal gaps and cracks to prevent future air leaks. Then, they install new insulation—spray foam, cellulose, or fiberglass—based on the home’s layout and climate needs. The entire process takes about one to two days, with minimal disruption to your daily routine.
The Return on Investment of Quality Insulation
Improving your home’s insulation is a practical upgrade that delivers long-term value. Attic insulation is among the top home improvement projects for return on investment, with Realtor.com reporting recouped costs of up to 107 percent or more at resale.
For homeowners in Wisconsin, proper insulation is especially appealing to buyers familiar with the region’s long heating season and humidity-driven summers. A well-insulated home signals lower utility costs, fewer drafts, and less wear on HVAC systems, all of which make a strong impression during a home inspection or showing.
Beyond the resale value, the monthly return is just as compelling. On average, ENERGY STAR estimates homeowners can save 15 percent on heating and cooling costs. These savings continue for the home’s life.
Unlike many home improvements that require ongoing maintenance or updates, insulation is largely a one-time upgrade that delivers consistent returns year after year. It’s a quiet but powerful upgrade for your energy bills and your home’s equity.
Next Steps for a More Efficient, Comfortable Home
Understanding the connection between insulation and HVAC performance is key to maintaining a comfortable, energy-efficient home. By improving your insulation, you’ll reduce your heating and cooling costs, extend the life of your HVAC system, and generate a more relaxed living environment.
If you’re ready to improve or assess your home’s insulation, contact A-Rite Construction. Our team can identify problem areas and perform high-quality replacements. Don’t wait—start making improvements today before extreme weather puts your home to the test.